
Example of import substitution: how to substitute an ink jet marker
Develop a conveyor laser machine to mark window profiles
Goals
One of the production stages at the BRUSBOX company is the date and batch number marking on window profiles. Previously, this process was made using an inkjet printer, but after the sanctions were imposed, servicing imported equipment became problematic and the price of ink increased, so the company was forced to look for an alternative product on the Russian market.
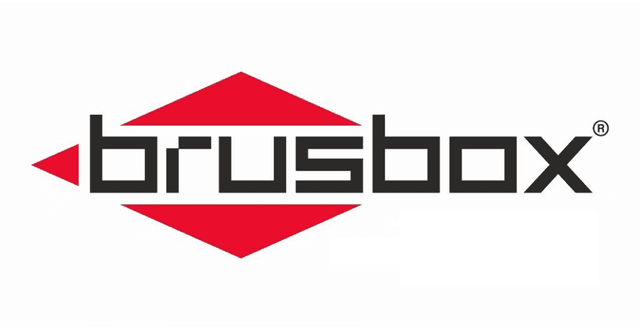
Solution
Before cooperating with LASSARD, the major costs associated with inkjet equipment were ink and solvents. Laser would help to eliminate these costs, as it does not need consumables. For this reason, BRUSBOX became interested in our proposal to develop a laser engraver that could be seamlessly integrated into the production line.
Our specialists created a prototype that was approved by the company management. While previously it was necessary to change cartridges, continuously monitor that the printing runs without problems, and erase the ink with a solvent and restart the line in case of a failure, with a laser it is only required to replace the lens and protective glass once every few weeks.
We take into account another important point. The enterprise operates around the clock, in 4 shifts, so our specialists configured the equipment parameters in such a way that to start a shift the operator only needs to press one button.
Result
LASSARD have supplied 20 laser marking systems for the BRUSBOX conveyor and named this model GRAVER LINE. According to the production director, the workflow has been 'significantly simplified.'
We have also supplied one spare unit, and four more ready ones are stored in our warehouse to ensure uninterrupted operation of the line in case of failure.
See more details about how we integrated the GRAVER LINE into the BRUSBOX conveyor in the video:
Call or email us
On weekdays from 9 am to 6 pm. Our phone number is +7 495 120 68 86, you can also message us in the chat.
Visit the demonstration
In the showroom or online. You'll get to know all the details of working with laser technologies.